Albion Mark™
Peter Johnsson Museum Collection™
Tritonia™
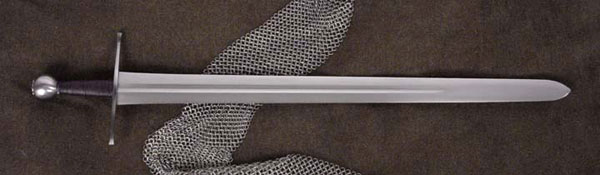
A
faithful recreation of an historical sword named after its find site,
an area now known as "Tritonia" in the medieval part of Stockholm, Sweden.
An archaeological excavation at the site yielded the remnants of a pier,
and this extraordinary sword.
It was still in its scabbard and remarkably intact when it was awakened
from its sleep in the muddy clay of the medieval shoreline (missing only
part of one arm of the cross-guard, a section of the point and the organic
portions of the grip). The original sword is now on display at the Museum
of Medieval Stockholm, Sweden.
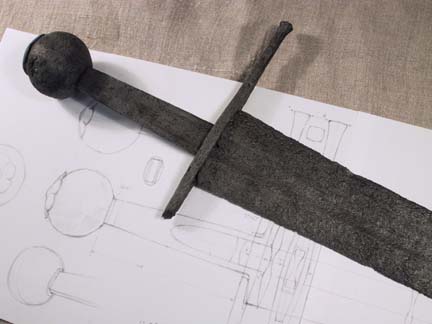
The
sword is a stunning eye-catcher and presented many interesting challenges
during the process of reconstruction. It was obviously made by a master
of the craft and combines awesome cleaving power with agility and speed.
Despite its hefty weight it is smooth and responsive in handling. Its
blade, tang, cross and pommel were skillfully forged with a good eye for
beautiful proportions and a deep understanding of the dynamic qualities
of a broad slashing sword of such imposing dimensions. A distinguishing
feature is how the distal taper is designed to give support and stiffness
to the thin cutting section of the blade.
A
very similar sword with the same broad blade and spherical pommel is seen
in a sculpture in the “Easter Shrine” of the Cathedral, Constance, dated
to 1300, depicting a soldier sleeping by the tomb of Christ. Weapons like
these were effectively wielded from horseback and were popular during
the later part of the 13th C and the first half of the 14th C.
The
sword made in the workshops of Albion is a direct result of a project
for the Museum of Medieval Stockholm. Swordsmith Peter Johnsson was commissioned
to forge an exact reconstruction that was to be exhibited alongside the
original.
The knowledge gained during this project is now resulting in a faithful
and highly realistic reconstruction made by the skilled artisans of Albion.
No effort is spared to make the swords true to the original not only in
dimensions but also in performance and aesthetic details.
The
blades are hand-ground and finished to a high satin finish. Each blade
is individually heat treated in Albion's Shop for maximum flexibility
and cutting performance. All of our blades are thoroughly tested to destruction
to ensure that they are as durable (or more) than a period original (see
the results of one such testing session here.).
The wooden core of the grip is bound with cord and covered with leather.
The cross with its gently flaring ends, its ball pommel and florette are
all hand finished and mounted to fit individual blades.
Specifications
Overall length: 39" (99 cm)
Blade length: 33" (83.8 cm)
Blade width (at base): 2.5" (6.35 cm)
COG: 4.75" from cross (12 cm)
COP: 22" from cross (55.9 cm)
Weight: 3 lbs 6 oz (1.53 kilos)
Read
Customer Testimonials about the Tritonia here.
Read
a hands-on review
of the Tritonia on myArmoury.com
Tritonia
Type XIIIb.... $1628
Convenient
payment plans are available for qualified
customers
This
sword is offered in a limited edition
of 1,000 swords worldwide.
Handmade
scabbard designed by Peter Johnsson, in a style popular in the late 13th
C early 14th C.
See photos and complete description here.
Tritonia Scabbard.... $1,200
Read an impartial review by Patrick Kelly of the Tritonia Sword at
myArmoury.com:
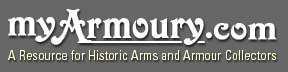
|
Peter
Johnsson on The Tritonia
|
Peter
Johnsson's original reconstruction of the Tritonia (and scabbard),
on display with the original sword at
the Museum of Medieval Stockholm
|
"This
sword is a big one.
The blade is broad and bold, yet still graceful. It is definitely
one of the largest single hand swords I have handled.
The original weighs some 1.4 kilos, even as one arm of the cross
and a piece of the point is missing.
The first impression when I saw it was its imposing size and beautiful
proportions. There is a crispness in the forging of pommel, tang
and cross.
The blade has interesting dimensions. At the base the width flares
gracefully. Along the rest of the blade it tapers only very little
from around four inches from the cross to the point. This lends
a dynamic quality to the design.
The real interest is in the way its distal taper is defined. It
is not straight but varies so that the stiffness in the middle is
optimized while the point area is as light as possible without compromising
strength. This also helps handling characteristics.
A wide, long and rather heavy sword like this needs a careful distribution
of mass not to become cumbersome.
The study of this sword gave valuable new insights to this problem.
It is a very worn slogan, but this sword really needs to be handled
to be appreciated. Its weight and responsive balance makes it very
aggressive in cutting.
I would guess that this was a cavalry weapon, perhaps even a knightly
sword judging by its quality and understated elegance.
We held a little cutting session with tatami mats in the Albion
workshops when I delivered the prototypes. The prototype Tritonia
sliced through single, double and triple mat rolls with equal ease.
It was possible to make good clean cuts some 6-7 inches apart, both
diagonally and horizontally.
Judging from these tests, it is clear that a clean hit with this
sword would be devastating.
I would like to say though that the real value in the making of
this sword was not to produce a sword that is a excellent cutter,
but to find a way to translate the working procedures from my smithy
to the workshops of Albion.
There are critical but subtle details in the shaping of the blade
and the managing of mass distribution and balance that puts high
demand on the skill of the craftsmen involved and the production
methods.
At first I was not thrilled about the spherical pommel, but it is
a typical feature on some of the Scandinavian swords of this period.
Before long I found myself having no reservations to its pommel.
It looked just right and I would not want to replace it to something
else. A wheel pommel on this sword would make it more mainstream.
It would loose much of its personality.
The pommel of the original is solid and clearly forged, not cast.
The hole that takes the tang is slightly too wide (by a millimeter
or so on each face of the tang). This gap is wedged with thin wooden
slats that are well preserved and still clearly visible.
This very slight "hollowness" is something we have taken into account
in the making of the reconstruction at Albion. Not having a hole
so large that wedges are needed, but by removing a slight amount
of material down the centre of the pommel, the tang is still firmly
wedged in place from the base to the rivet and we still get the
balance right.
After having worked with the Tritonia on and off for more than two
years it has sort of passed beyond liking or not liking. Of course
I am fascinated with it and love it, but it has rather taken a place
among the extended family, so to say.
The Tritonia has taught me some important things and because of
that I am eternally grateful to its original maker (or makers).
The sword as a whole has very impressive proportions and is clearly
the result of the work of a master craftsman. As such it merits
a closer look.
To
put into production a sword at custom quality level that is constant
not only in dimensions, but also true to the idea of the original
sword when it was new, is challenging.
It has been an interesting and very inspiring period working as
a consulting swordsmith and designer with Albion. I hope that you´ll
find these swords an interesting addition to what is available on
the market today."
|
|
--
Peter Johnsson
|
|